Das Hochregallager als Herzstück
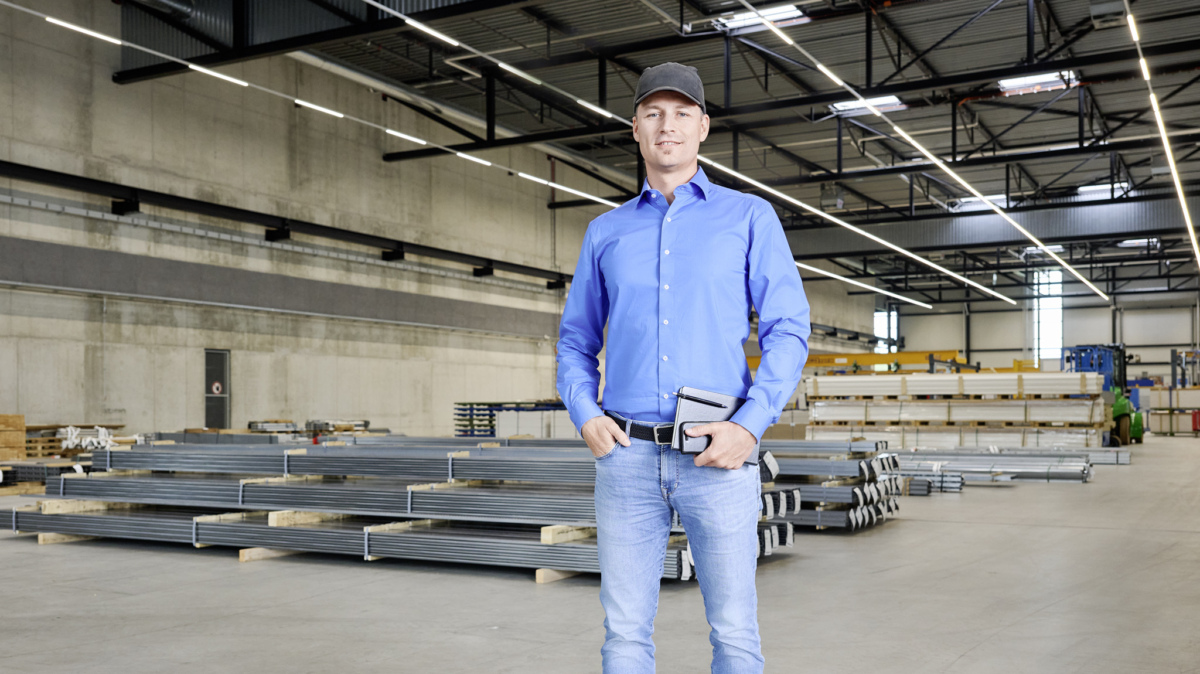
Fabian Strim, was macht das Forster-Hochregallager so besonders?
Das Hochregallager ist das Herzstück der Produktion und Logistik, denn alle Warenbewegungen mit Profilen sind ans Hochregallager angebunden. Wir arbeiten nach dem Prinzip «Ware zum Mann» – und nicht umgekehrt. Dies alles geschieht automatisch an mehreren Ausgabestationen. Hinzu kommt, dass auf einer kleinen Grundfläche sehr viel Lagervolumen gewonnen wird. So wird weniger Grundstückfläche beansprucht und Bodenressourcen können effizienter genutzt werden.
Solch ein ausgeklügeltes System kostet.
Ja. Die Kosten für ein Hochregallager in einer solchen Dimension setzen sich aus verschiedenen Komponenten zusammen. Da wir relativ hohe Lasten im Hochregallager haben, müssen auch ein entsprechendes Fundament und stabile Wände betoniert werden. Selbstverständlich musste auch der Untergrund entsprechend verdichtet werden. Dies allein macht schon einen grossen Kostenanteil aus. Weiter besteht das Hochregallager aus einem massiven Stahlbau und 5156 Kassetten sowie zwei Bediengeräten. Diese werden aufgrund der Grösse und der Leistung benötigt. Selbstverständlich ist das Hochregallager komplett an unser ERP-System angebunden.
Neben Kosten mussten Sie sicher auch andere Herausforderungen bewältigen.
Die Herausforderungen waren mannigfaltig. Primär galt es, das Konzept des Hochregallagers zu definieren. Dies erfolgte auf den drei Säulen Ansprü-che, Simulationen und Referenzbesuche. Nach der Konzeption galt es, den bestmöglichen Standort innerhalb des Produktionsgebäudes zu evaluieren. Entscheidend für den Standort war der komplette Materialfluss vom Inbounding über die Produktion bis zum Outbounding – um ein Beispiel zu nennen für einen optimalen Warenfluss in der Logistik. Ein weiterer Punkt war die Definition für die ideale Auslegung der Kassettengrösse, um das Lagervolumen maximal auszunutzen. Eine Challenge auf baulicher Seite war die Anforderung an die Ebenheit der grossen Grundfläche für das Hochregallager von rund 100 × 22 Metern. Beim Aufbau war der Zeitplan der Fertigstellung des Hochregallagers und der anschliessenden Befüllung die grösste Herausforderung.
«Die Mitarbeitenden spielen immer noch eine zentrale Rolle.»
Gab es weitere technische oder gestalterische Vorgaben, die das Hochregallager erfüllen musste?
Natürlich gab es diese. Wichtige technische Vorgaben waren für uns die Lagerkapazitäten, die Zykluszeiten und die Beladung pro Lagerkassette. Um hier sicherzugehen, wurden diese Anforderungen mittels Simulationen und Berechnungen überprüft. Das neue Hochregallager wurde so konzipiert, dass es vom Aussenbereich nicht sichtbar ist. Zudem wurde es einige Meter in den Boden gebaut. Das hat zugleich die ganze Produktionshalle stabilisiert – und dadurch musste der Untergrund nicht gepfählt werden.
Die Sicherheit des Systems ist eine Sache. Doch wie ist die Sicherheit der Mitarbeitenden gewährleistet?
Das Hochregallager entspricht den neuesten Sicherheitsvorschriften. Alle Lagerstationen sind mit mehreren Lichtschranken gesichert, wodurch die Zutrittsüberwachung gewährleistet wird. Zudem sind im Inneren des Hochregallagers Rauchmelder, ein Wärmeabzug sowie eine Sprinkleranlage für den Brandschutz installiert. Ein wichtiger Teil der Arbeitssicherheit ist die Information und Schulung der Bediener und des Wartungspersonals. Für die Wartung der Anlage werden speziell ausgebildete Industriekletterer beigezogen.
Können Sie uns kurz erklären, wie das Lager funktioniert?
Im Zentrum stehen zwei Regalbediengeräte, die zwischen zwei Lagergestellen hin- und herfahren und unabhängig voneinander Aufträge erledigen. In diesen Lagergestellen sind sogenannte Lagerfächer, die neben- und übereinander aufgebaut sind. Der Aufbau ist vergleichbar mit Bienenwaben, daher stammt auch der entsprechende Name – «Wabenlager». In jedem Lagerfach wird eine Kassette gelagert, die mit dem Regalbediengerät aus den Fächern gezogen und an einer Ausgabestation abgegeben wird. Das Hochregal verfügt über eine Lagerkapazität von mehr als 5000 Lagerfächern, wobei eine Kassette mit 2500 kg belegt werden kann. Die Lagerfächer haben wir in unterschiedliche Lagerzonen eingeteilt, damit die Produktionsanlagen und die Ein- und Auslagerung optimal angefahren werden können. Entstanden sind sogenannte Vorlagerplätze für Material. Diese Vorlagerplätze werden am nächsten Tag für den Versand benötigt. Mit dieser Einstellung werden die Kassetten bei freier Verarbeitungskapazität des Hochregallagers automatisch für den Versand umgelagert.
Das vereinfacht den Arbeitsalltag sehr.
Auf jeden Fall. Die ganze Automatisierung leistet hervorragende Arbeit und entlastet unsere Leute. Die angeforderte Langgutware wird schnell an der Ausgabestation bereitgestellt, ohne dass der Mitarbeitende mit Hebemitteln arbeiten muss. Wir erreichen mit diesem automatisierten Warentransport einen hohen Grad an Arbeitssicherheit und können unsere Effizienz zudem steigern. Ausserdem führt das System eine automatische Zuweisung des Materials zum Auftrag durch, wodurch die händische Kommissionierung entfällt.
Text: Fabian Alexander Meyer
Bild: Thomas Hary