Im Stop-and-go-Modus zum Erfolg
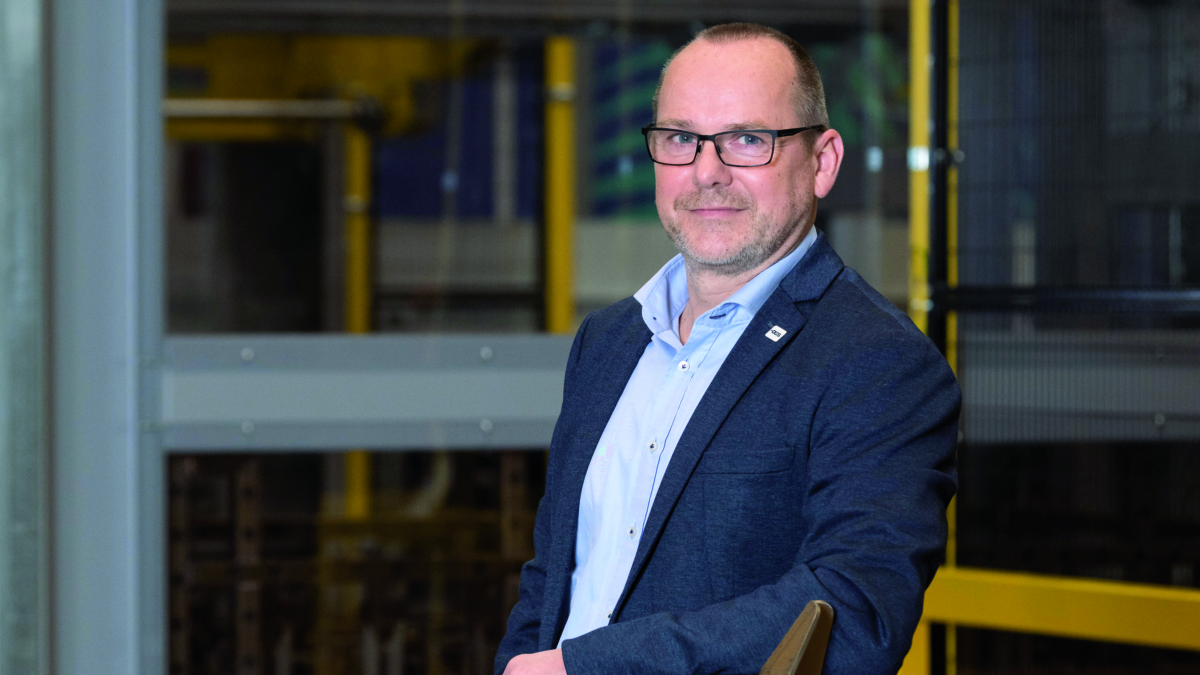
Die DGS Druckguss Systeme AG mit Hauptsitz in St.Gallen fertigt aus Aluminium- und Magnesium-Legierungen komplexe Druckguss-Komponenten. Das Unternehmen beschäftigt 440 Mitarbeiter im Werk in Winkeln, 440 in Tschechien und weitere 360 in zwei Werken in China. Die Produkte der DGS gehen zu 97 Prozent in die Automobilindustrie – jedes Husten dieser Branche erlebt der Zulieferer deshalb unmittelbar.
Arbeiten wie im Stau
Fragt man DGS-CEO Andreas Müller, wie sich die Verwerfungen der Weltwirtschaft aufgrund gebrochener Lieferketten auf sein Unternehmen auswirken, sagt er: «Das letzte Jahr war das verrückteste, das ich in meiner ganzen Berufslaufbahn erlebt habe.» 2020, das erste Corona-Jahr, sei im Vergleich noch relativ einfach zu handhaben gewesen. Auch wenn die Kunden, vor allem die bekannten deutschen Autohersteller, ihre Werke schlossen. «Damals wussten wir, dieser Hersteller macht drei Wochen zu, jener vier – dann schliessen wir also auch drei Wochen, nachdem wir vielleicht zuerst noch produziert hatten, bis alle Lager voll sind, um nicht ins Stottern zu geraten.» Das Jahr 2021 ist nun genau von einem Stotterbetrieb geprägt, ein mühsames Stop-and-go. «Das ist wie beim Stau», umschreibt Andreas Müller den Effekt, «aus manchmal unerfindlichen Gründen, weil ein Auto zu viel gebremst hat, bildet sich ein Stau, der sich dann auch ganz unkoordiniert wieder auflöst. Ich denke, so ist das auch mit den Lieferketten.» Im Vorjahr, als es noch keinen Mangel an Chips und keine unterbrochenen Lieferketten gab, konnten temporäre Werk-Stilllegungen besser mit den Kunden und der ganzen Branche synchronisiert werden.
Die ganze Kette gerät ins Stocken
Wenn die Autoindustrie ein Teil nicht bekommt, frage sie auch andere nicht nach: «Wenn nur ein Lieferant einen bestimmten Chip nicht liefert, kommt die ganze Kette ins Stocken.» Dass die globalen Lieferketten fragil und komplex sind, habe man gewusst, «aber irgendwie hat es funktioniert, es hat für alle Marktteilnehmer gepasst». Stoppt ein Autohersteller seine Produktion, produziert ein Lieferant weit hinten in der Kette, der seinerseits Lieferanten zuarbeitet, vorerst weiter, bis alle Stufen ihre Lager gut bestückt haben. Dann aber muss der Unterlieferant vielleicht Monate warten, bis die Produktion weitergeht. Die Kette gerät ins Stocken, auch die Rohmaterialbeschaffung wird runtergefahren. Legt dann der Autohersteller wieder los, braucht es eine Weile, bis auch die Rohmaterialbeschaffung am anderen Ende der Lieferkette wieder auf Touren kommt. Schafft sie es nicht rechtzeitig, kann dies die nächsten Unterbrüche provozieren. «Hier gibt es so viele Abhängigkeiten, dass man das gar nicht richtig durchdringen kann», sagt Andreas Müller. Der Stotterbetrieb und die daraus entstehenden Unsicherheiten hätten die DGS weitaus mehr belastet als das erste Corona-Jahr 2020.
«Wenn ein Container statt 2000 Dollar 17 000 Dollar kostet, dann schlucken wir das.»
Kurzfristiger Produktionsstopp
Mehrfach wurde die DGS im letzten Jahr von einem Automobilhersteller extrem kurzfristig darüber informiert, dass ein Werk für ein bestimmtes Automodell für mehrere Wochen stillstehen werde, im extremsten Fall traf die Ankündigung gerade einmal zwei Arbeitstage vor dem Stopp ein: Ein komplettes Werk, das mit DGS-Teilen aus St.Gallen und Tschechien beliefert wird, schloss für vier Wochen. «Wir hätten während dieser Zeit jeden Tag eine Auslieferung und entsprechend einen stabilen Umsatz gehabt.» Ohne wirkliche Vorwarnung wurden «Unmengen an Abrufen storniert und damit geplante Umsätze nach hinten geschoben», wie Müller erklärt: «Wir hatten also immer einen guten, grossen Auftragsbestand, der nun wie eine Bugwelle vor uns herschwappte.» Die jeweiligen Autohersteller hätten stets bis zuletzt versucht, alle notwendigen Teile zu bekommen, um ihre Autos zu bauen. Sie liessen ein Werk bis im letzten Moment laufen, um nicht den Lieferanten das Gefühl zu geben, dass nicht produziert werde – um eben kein nächstes Loch in der Lieferkette zu provozieren. «Die Hersteller haben Bestände gehortet, solange es irgendwie ging, und dann hat doch ein Schlüsselteil gefehlt, worauf sie ihr Werk schlossen.»
«Wir stellen die richtigen Produkte her.»
Auch wenn ein Lieferant ausfiel, hätten die Autohersteller die anderen Zulieferer «auf Zug gehalten», damit sie immer bereit sind, zu liefern. «Das hat uns letztes Jahr schon ganz schön beschäftigt», sagt Müller. 2021 hat die DGS während einer Woche Kurzarbeit eingeführt, ansonsten normal gefertigt – aufgrund des Stotterbetriebs mit den extrem kurzen Vorwarnzeiten war eine vernünftige Pause nicht planbar. Im Jahr davor hatte die DGS mehrere Wochen Kurzarbeit planen können, «damals hatten so ziemlich alle Hersteller gleichzeitig einen Shutdown vorgenommen.» Jetzt sind es einzelne Werke oder Fahrzeuglinien, die spontan gestoppt würden. «Wenn ich heute weiss, dass ein Werk in zwei Tagen dicht macht und ich es nicht beliefern kann, dann muss ich mich trotzdem bei den anderen Kunden darauf einstellen, dass sie noch bestellen und beliefert werden wollen.»
Auch interessant
Warten auf das letzte Teil
2021 wurden von den grossen Autoherstellern Hundertausende von Autos gebaut, die nicht ganz fertig waren, es fehlten beispielsweise Fensterhebermodule oder Radios, die noch nachgerüstet werden mussten. «Die haben die nigelnagelneuen Autos auf den Hof gestellt und gewartet, bis das letzte, noch fehlende Teil eingebaut werden konnte», beschreibt Andreas Müller die Situation – die auch die Autoriesen zum Improvisieren zwang: «Ich habe von einem Hersteller gehört, dem ein Türschliessmodul fehlte und der deshalb 100 000-Euro-Fahrzeuge nicht bauen konnte», sagt Müller. In solchen Fällen würde ein Hersteller auch einmal seine Konstruktion ändern, um Teile einzubauen, die beschaffbar seien. Die DGS ist in jeder Beziehung nahe bei ihren Kunden, da sie hauptsächlich Teile für die Rohkarosserie eines Fahrzeugs direkt an die Hersteller liefert, also die ersten Teile, die im Produktionsprozess zusammengeschweisst werden. «Unsere Komponenten werden sehr früh in der Produktion verbaut, dadurch bekommen wir jeden Shutdown eines Werkes sehr unmittelbar mit», erläutert der DGS-CEO.
Nadelöhr Logistik
Die Kunden selbst haben bei sich von einem bestimmten Teil ein kleines Lager. Zusammen mit den Teilen, die auf der Strasse sind, also in der Anlieferung, reicht dieser Bestand für vielleicht drei Wochen. Bei der DGS stehen im Schnitt noch nicht spedierte Teile für etwa eine Woche Produktion, die Autoproduktion könnte also noch vier Wochen laufen, wenn die DGS keine neuen Teile mehr herstellt. Damit die DGS die verschiedenen Komponenten wie gewünscht produzieren kann, ist sie ihrerseits auf Lieferanten angewiesen, insbesondere auf die der Rohstoffe Aluminium und Magnesium. Doch nicht nur die Verfügbarkeit eines bestimmten Vorprodukts kann die Lieferketten sprengen, auch die Logistik kann das fein austarierte internationale Netzwerk Makulatur werden lassen. Bis zur Pandemie hätten Transporte von und nach China reibungslos funktioniert, sagt Andreas Müller, «das Angebot war immer da, ein Transport war immer machbar und immer planbar». Der Preis für den Transport eines Containers lag zwischen 1500 und 2000 Dol- lar. «Heute kosten die Transporte aus China etwa 13 000 bis 17 000 Dollar – also fast das Zehnfache.» Dazu kommt, dass in China mehrfach Häfen aufgrund der Pandemie geschlossen wurden – Schiffe fuhren nicht, Transporte waren nicht verfügbar, Logistiker mussten Alternativ-Häfen suchen. «Wirklich verrückte Zeiten!», meint der DGS-CEO; im Wissen, dass diese Zustände noch längst nicht überwunden sind.
Engpass bei Magnesium
Beim Rohmaterial selbst erlebt die DGS ebenfalls turbulente Preissteigerungen und Lieferengpässe. Magnesium, das zu 90 Prozent aus China importiert wird, weil es kaum noch andere Produzenten gibt, kostete bisher rund 2000 Dollar pro Tonne. Dieser Preis kletterte innert kürzester Zeit auf 12 000 Dollar, der Rohstoff hat sich also um einen Faktor sechs verteuert. Inzwischen ist der Preis etwas gesunken, er verharrt aber immer noch auf hohem Niveau.
«Heute kosten die Transporte aus China fast das Zehnfache.»
Die DGS konnte dank enger Lieferantenbeziehungen und vorausschauender Planung eine Materialknappheit im eigenen Werk verhindern, «im Markt herrschte aber teilweise Panik», sagt Andreas Müller. In dieser Situation kam der DGS entgegen, dass sie ohnehin geplant hatte, ihren globalen Einkauf zu stärken und die Geschäftsleitung direkt in die strategische Beschaffung involviert ist. Immerhin gibt es in den Verträgen mit den Autoherstellern Materialanpassungsklauseln: Der Preis fürs Rohmaterial wird angepasst, «aber stets mit einem zeitlichen Versatz von drei oder sechs Monaten», jedoch nicht alle Kostenkomponenten, wie Andreas Müller erklärt. Somit können einige Preissteigerungen, jedoch nicht alle, weitergereicht werden; sie müssen aber vorfinanziert werden. Anders verhält es sich bei den Logistikkosten. «Wenn ein Container statt 2000 Dollar nun 17 000 Dollar kostet, dann schlucken wir das derzeit zu 100 Prozent.»
Strompreis vervielfacht sich
Als sehr energieintensive Industrie macht der DGS auch eine weitere Entwicklung Bauchweh: «In St.Gallen und in Tschechien ist die Energie 2022 sechsmal teuer als im Vorjahr.» Dies, weil der europäische Strompreis wenig mit der Schweiz zu tun habe, wie Andreas Müller erklärt: «Die Gaspreise sind explodiert, und daran sind auch die Strompreise gekoppelt, egal, wieviel regenerativen Strom ich einkaufe.» In St.Gallen verbrauche die DGS 35 Gigawattstunden Strom und 15 Gigawattstunden Gas im Jahr, was in der Bilanz etwa vier Prozent entspräche. «Wenn diese vier Prozent sich plötzlich vervielfachen – in einer Branche, die im Durchschnitt sowieso nur im niedrigen einstelligen Prozent-Bereich verdient –, dann kann man sich ausmalen, was gerade passiert», hält Müller fest. Unter dem Strich bleibt ein beträchtlicher Teil der Preissteigerungen bei Zulieferern wie der DGS hängen. «Wir schreiben wie die ganze Zulieferbranche deutlich schlechtere Ergebnisse – während die Autohersteller deutlich bessere Ergebnisse erzielen. Das ist der Frust für uns.» Die OEM (Original Equipment Manufacturer), wie in der Autoindustrie die Fahrzeughersteller genannt werden, hätten zwar auch massive Rückgänge gehabt, «aber die OEM haben einfach ihre Rabatt-Programme eingestellt, denn die Nachfrage nach Autos ist immens. Wenn ein Autohersteller seine Rabattschlachten einstellt, verdient er schnell mal zehn Prozent mehr.» Dazu komme, dass die Hersteller sich auf margenträchtige Fahrzeuge fokussiert hätten, wie Müller darlegt. «Die OEM bauten primär die renditestarken Fahrzeuge und haben dabei trotz schlechter Umsätze offensichtlich Rekordgewinne eingefahren. Wir Lieferanten arbeiten im Stotterbetrieb und haben die gleichen Saving-Forderungen wie immer auf dem Tisch.»
Auch interessant
«Das letzte Jahr war das verrückteste, das ich in meiner Berufslaufbahn erlebt habe.»
Beim Elektroauto-Trend dabei
Neben grundsätzlich renditestarken Modellen pusht die Autoindustrie auch Elektrofahrzeuge – nicht zuletzt, um den CO2-Ausstoss der Gesamtflotte zu senken, weil sonst empfindliche Bussen drohen. Diese Entwicklung kommt der DGS entgegen: «Wir haben uns sehr früh auch auf neue Technologien konzentriert», sagt Andreas Müller und weist auf die neue Produktionshalle der DGS im St.Galler Stadtteil Winkeln: «In der neuen Halle laufen eigentlich ausschliesslich Teile für Elektro-Fahrzeuge. Und die laufen gut. Die Produktionen eines Porsche Taycan oder eines Audi e-tron GT laufen auf Kammlinie.» Natürlich werden auch in Elektroautos unzählige Chips verbaut. Die Hersteller geben die Chips, die sie bekommen, im Zweifelsfall aber bevorzugt in solche Autos statt in Verbrenner. Auch für elektrische Mercedes-Modelle stellt die DGS Teile her, für den EQS etwa Batterieteile, für die elektrische A- und B-Klasse Aggregaterahmen – jenes Bauteil, das praktisch den kompletten Motor samt Wärmepumpe, Klimagerät, Kältemittel, Verdichter und weitere Komponenten aufnimmt. Daimler ist inzwischen der grösste Kunde, für alle Mercedes-Benz-Limousinen von der A-Klasse bis zur S-Klasse stellt die DGS beispielsweise mehrere Bauteile für die Lenksäule her, im Peak waren es 1,8 Millionen Sätze komplexer Magnesium-Teile. Für den Kunden Audi hat die DGS in den letzten Jahren fast für jedes Modell Teile geliefert, inklusive der hochpreisigen Modelle wie R8 oder der zu Audi gehörenden Sportwagenmarke Lamborghini.
Teile werden immer grösser
Die mit Druckguss-Verfahren hergestellten Teile werden immer grösser, in Winkeln ist unter anderem eine Maschine mit 4400 Tonnen Schliesskraft im Einsatz. Die Maschine wurde angeschafft, als sich die DGS einen ersten Auftrag für riesige Strukturgussteile sicherte, heute werden etwa ganze Batteriegehäuse auf ihr gegossen. Für die zusätzlichen und grösseren Maschinen hat die DGS dann auch die komplett neue Halle errichtet. Gleichzeitig mit der Zukunftssicherung am Standort St.Gallen investiert die DGS auch in Tschechien und China in neue Werke. «Wir stellen die richtigen Produkte für die Fahrzeuge her, die gut gelaufen sind», resümiert Andreas Müller. Damit dies so bleibt, muss das Unternehmen wohl weiter investieren: «Wir haben einige Innovationsthemen am Laufen, um noch grössere Gussteile machen zu können.» Tesla habe mit Giga-Casting den Trend zu noch grösseren Bauteilen befeuert und fertigt bereits den ganzen Hinterwagen aus einem einzigen Gussstück. Bisher wurden dafür rund 70 Guss- und Blechteile verschweisst. Der Guss aus einem Stück verbilligt die ganze Autoherstellung, im Rohbau der Karosserie fallen bei Tesla Hunderte von Robotern weg. Es dürfte deshalb nicht lange dauern, bis die deutschen Autobauer nachziehen.
Produktivität sinkt
Am Standort St.Gallen produziert die DGS die Teile für die Autoproduktion inzwischen auf 23 imposanten Giessmaschinen. Etwa 200 verschiedene Produkte werden aktuell mit diesem Maschinenpark hergestellt, «wir sind also ohnehin stets in einem Umrüstzyklus», sagt Andreas Müller. Wenn Teile für ein bestimmtes Fahrzeugmodell plötzlich nicht nachgefragt werden, können andere produziert werden. In der Fertigbearbeitung gibt es allerdings Linien, die für spezifische Produkte eingerichtet sind und in einem solchen Fall stillstehen. Das Personal dieser Linien wird nach Möglichkeit bei anderen Produkten eingesetzt, allenfalls wird auch eine Woche Kurzarbeit angeordnet. Meistens bauen die Leute aber noch bestehende Überstunden ab oder beziehen regulären Urlaub. «Kostenmässig haut das ganz schön rein», sagt Andreas Müller. «Wenn ich ständig Mitarbeiter jonglieren und in diesem Stotterbetrieb-Modus arbeiten muss, dann sinkt automatisch die Produktivität.»
Interne Kommunikation ausgebaut
Auch für die Stimmung im Betrieb ist diese Situation eine Belastung. Die Führungskräfte bräuchten viel Fingerspitzengefühl, obwohl bei ihnen selbst die Nerven zuweilen blank lägen: Sie müssen antizipieren, was die Kunden wollen, gleichzeitig kommen die Ergebnisse unter Druck und die Mitarbeiter sind unzufrieden, weil es nicht rund läuft. Als Gegenmassnahme wurde in der DGS die interne Kommunikation deutlich verstärkt, es wurde eine elektronische Plattform eingeführt, über die nun alle Mitarbeiter die Firmennews auf ihr Handy bekommen. «Eine Massnahme, die wir schon länger geplant hatten, aber immer vor uns herschoben. Das haben wir aufgrund von Corona dann innert zweier Wochen umgesetzt», sagt Andreas Müller. Nun kann die DGS auch jene Angestellten erreichen, die im Urlaub oder wegen Kurzarbeit nicht im Betrieb sind. «So haben wir eine gute Bindung zu den Mitarbeitern aufgebaut.» Die persönliche Kommunikation ersetze dies nicht, der neue Kommunikationskanal sei aber eine deutliche Verbesserung gegenüber früher.
«Wir haben einige Innovationsthemen am Laufen, um noch grössere Gussteile machen zu können.»
Zu kommunizieren hat der Chef trotz aller Widrigkeiten einen durchaus positiven Blick in die Zukunft. «Wir machen keine Antriebsteile für Verbrenner, aber wir sind bei den Elektrofahrzeugen auch in den Antriebsteilen vertreten. Das gab es vorher nicht, das ist ein neues Segment. Deshalb sind wir 2021 auch zehn Prozent gewachsen, wir haben Umsatz zugelegt gegenüber dem ersten Corona-Jahr.